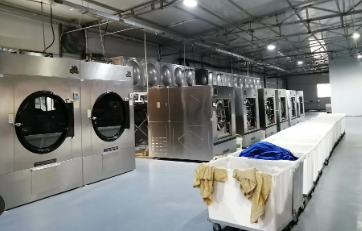
Different types of garment washing, their working techniques, washing recipes and washing process flow chart
Washing: Generally, washing means cleaning dirt and dust with water, chemicals and soap. But washing is a term that carries a significant meaning in garments. Washing is a process used to alter or modify the look, appearance, comfort and feel.
Washing purpose:
1. To change the aspect or appearance.
2. To clean the garment.
3. Removing waste matter, dust, dirt from clothes
4. Make clothing’s comfortable.
5. To make clothes soft and easy.
6. Making clothes wearable after purchase.
7. Make clothes look old.
8. To detoxify clothing.
Washing Type:
Mainly two types of washing are done-
(i) Wet washing process
(ii) Dry washing process
Wet Washing Process: Wet washing process is a process where water, liquid chemicals are used in washing at a specific temperature according to a recipe. Wet washing process is divided into-
(a) General washing
(b) Pigment wash
(c) Enzyme wash
(d) Stone washing
(e) Bleach wash
(f) Bleach stone wash
(g) Acid washing
Dry Washing Process: This process is a type of process where no water is used in washing. The process of dry cleaning is classified as-
(a) Sandblasting
(b) Whispering
(c) Hand scraping
(d) PP spray
(e) Destruction
(f) Grinding
For both denim and non-denim washing standards follow the following procedure.
Dry Washing Process Flow Chart:
Receive garments
↓
QC
↓
Find out sewing problems and test measurements
↓
sparkling
↓
Hand sanding
↓
tagging
↓
Final QC
↓
1st wash
↓
Hydro
↓
dryer
↓
QC
↓
grinding
↓
destroy
↓
PP spray
↓
Send to wet wash
Wet Washing Process Flow Chart:
Garments received
↓
dry process
↓
Send wet wash
↓
Garment load in washing m/c
↓
Desizing
↓
enzyme
↓
Bleach (if needed)
↓
Neutralization
↓
Extracting
↓
to dry
↓
PP spray (if required)
↓
Neutralization
↓
Tinting (if required)
↓
Softener
↓
Extracting
↓
to dry
↓
3D
↓
cure
↓
Qc
↓
Delivery
Normal Wash: Normal wash is a cleaning process that removes dust, dirt and starch from the surface of the garment in solution form. It is an easy washing process.
General Washing Purposes:
1. Removal of starch from the surface
2. To remove dust and dirt from the body of the garment.
3. See, shine.
4. To feel soft hands.
5. To enable wear after purchase.
General washing steps:
Desizing
↓
to soften
↓
Hydro extract
↓
dryer
↓
QC and delivery
The steps are described with the recipe:
Step 1: Desizing: Desizing means removing the size material from the surface.
Let’s say, the batch contains 70 kg of twill/denim garments.
Recipe: M:L = 1:8
Detergent = 0.5 g/l
Temperature = 40-60˚C
Time = 5-10 minutes
Avoid alcohol
cold wash
Step 2: Softening: Garments are softened to soften for a soft hand feel.
Recipe:
M:L = 1:8
Time = 5-10 minutes
Temperature = 20˚C
Softener = 0.6 g/L
Acetic acid = 0.5 g/l
Discard the liquor
Unload the garment
Hydro Extract: In this step excess water is removed using a hydro extractor machine.
Dryer: Dryer is used to dry clothes.
Load the dryer
Temperature = 60-70˚C
Time = 40-50 minutes
And time for cold drying = 10-15 minutes
QC & Delivery: After drying the garments are checked and if ok, send to finishing.
Acid wash: Acid wash is the most common and popular washing process in the washing category. Acid washing is a process of partial bleaching with chlorine bleach. Pumice stone is often used in acid washing. Pumice stone is a lightweight stone produced from volcanic eruptions. Pumice stone is used as a brush. The action between the garment and the pumice stone surface creates a fading effect. The more action that occurs, the more fading will produce the effect and vice versa. To reduce costs and washing standards matching foam is used.
Purpose of acid wash:
1. Make clothes look old.
2. To improve tenderness.
3. To achieve customer value.
4. Increase frictional stiffness.
Acid washing steps: The following steps are maintained through the acid washing process.
Desizing
↓
hot wash
↓
Acid wash
↓
Cleaning
↓
Neutralization
↓
soft wash
↓
Hydro extract
↓
dryer
↓
Delivery
The steps are described with the recipe:
Let’s say there are 70 kg of twill/denim garments to be washed in the batch.
Step 1: Desizing: Desizing means removing the size material from the surface.
Recipe: M:L = 1:8
Detergent = 0.5 g/l
Desizing agent = 0.5 g/l
Temperature = 40-60˚C
Time = 5-10 minutes
Skip the liquor
Rinse with water
Step 2: Hot Wash: Hot wash is done to remove the adhering material from the surface of the garment.
Recipe: M:L = 1:8
Temperature = 50-60˚C
Time = 5 minutes
Skip the liquor
Dry the unloaded clothes
Step 3: Acid Wash:
o Water = 100 l
o Potassium permanganate = 1000 g
o Phosphoric acid = 250 g
o Stir the solution in a stainless steel tub with dry pumice stone.
o Soak the stone in the chemical solution for 10-20 minutes
o The stone-sorted solution is dried in open air for 2-3 hours
o Machine loads 35-40 kg pre-treated garments per batch
o Pre-treated stone is loaded into the machine.
o Start the machine and run for 10-20 minutes.
o After that unload clothes and stones separately. Stones with PP solution hit the clothes and discolor. Now load the clothes into another washing machine for the next step.
Step 4: Cleaning: Here washing is done to remove broken stone dust and chemical cleaning.
Recipe:
M:L=1:10
Detergent = 1 g/l
Time = 10-15 minutes
Temperature = 40-50˚C
Throw away the liquor.
Step 5 : Neutralization: Neutralize the acidity from the clothing.
Recipe: M:L=1:8
Meta bisulphate = 5 g/l
Time = 10 minutes
Temperature = 25-30˚C
Discard the liquor
Step 6: Softening: For soft and smooth handling, softening is done.
Recipe: M: L = 1: 8
Softening agent = 1gm/L
Acetic acid = 0.6 g/L
Drop the liquor and unload the clothes
Step 7: Hydro-extract: Removing excess water with a hydro extractor machine.
Step 8: Dryer: After taking out the clothes, load them in a steam dryer or gas dryer.
Temperature = 50-60˚C
Time = 40 minutes
Step 9: QC and Delivery: After drying the garments are checked. If OK, delivery will be made.
Enzyme wash
Enzyme Wash: Enzyme wash has become popular in the garment washing sector these days to reduce the adverse effects of stone wash. Enzymes are living biochemical substances and act as catalysts in the washing process.
There are two types of enzymes. Eg- (i) Neutral Enzyme (ii) Acid Enzyme
Neutralized enzymes are classified into powder form and liquid form.
Purpose of Enzyme Wash:
1. Removal of size materials
2. Remove starch materials.
3. Achieve high low friction on garments and seam friction in sewing area.
4. To achieve customer value.
5. To develop organic polishing effect of cotton.
6. Increase color fastness and rub fastness.
Enzyme washing step:
Desizing
↓
enzyme
↓
to soften
↓
Hydro extract
↓
to dry
↓
Delivery
Step 1: Desizing: Desizing means removing the size material from the surface.
Recipe: M:L = 1:8
Detergent = 0.5 g/l
Desizing agent = 0.5 g/l
Temperature = 40-60˚C
Time = 5-10 minutes
Discard the liquor
Rinse with water
Step 2: Enzyme Wash:
Recipe: M:L = 1:8
Acetic acid = 0.6 g/L
Anti back staining acid = 0.6 g/l
Acid Enzyme = 1.5 g/l
Temperature = 40-60˚C
Time = 40 minutes
Increase the temperature to 90˚C and run for 1 minute to kill the enzyme
Step 3: Softening: Garments are softened to soften for a soft hand feel.
Recipe:
M:L = 1:8
Time = 15-20 minutes
Temperature = 20˚C
Softener = 0.6 g/L
Acetic acid = 0.5 g/l
Discard the liquor
Unload the garment
Step 4: Hydro Extract: Remove excess water using hydro extractor machine.
Step 5: Dryer: After taking out the garments, load them into a gas dryer.
Temperature = 50-60˚C
Time = 40 minutes
Step 6: QC and Delivery: The garments are checked after drying. OK then delivery.
dry process
Whiskers: The first step in dry cleaning is the whisker. It is the most common and popular dry process. A separate design is made and then the design is transferred to a rubber board or pattern. After this, the pattern is placed inside the garment and scrubbed over the pattern where the design will be depicted.
Whiskers can be done in three ways.
(i) By Huskering pattern.
(ii) By manual hand scraping.
(iii) Using a laser machine.
Whispering Pattern:
1. First the design is selected then a white poly is placed on the garment
2. Mark the design with a marker along a seam line
3. Replace rubber buoy ninrd or pattern and rubber poly.
4. Make a design on a rubber board by carving with a cutter or knife.
5. The pattern is created.
6. Now it is inserted into the garment.
7. Scrape over the etched area and a whisker design is created.
Manual Hand Scrape:
Manual hand scraping is used to bring out the whispering pattern design on the garment. Abrasive paper or emery paper, pattern, chalk are used for manual hand scraping. There are variations according to the use of abrasive paper.
(i) P-400 (Very Ruk )
(ii) p-800 (medium rough)
(iii) P-1000 (very low roughness)
Laser Machine: Laser machine is used for sparkling or burning effect on denim garments. This process is done after washing.
Hand Scraping: Hand scraping is manual and widely used process in dry washing department. This process is applied after the fiskering process to remove color or fade specific areas. Abrasive paper, gum tape, air dummy, hands are used to do this. The pressure should be even when scraping the garment by hand.
Grinding:
A grinding machine is used to destroy the edge. Grinding is destroying the edges of the garment. It is often done on hems, pocket openings, pocket flaps of clothing. Small size stones are used in the machine for grinding.
Destroy:
Destruction is the most common and nowadays it becomes the most popular in the fashion market. To do this Roses pen grinding machine with stones of different sizes is used. Through this process, the white yarn or weft yarn is worn which makes the garment unique and fashionable.
3D Crinkle/Wrinkle:
Wrinkles or wrinkles carry the same meaning. This is the final process of dry wash If a customer requires this wash, it is done after completing all types of dry and wet wash For this process, all garments are washed with resin and then dried by hydro extractor. Then special effects are depicted. Denim, twill, poplin, knit, viscose, nylon etc. are wrinkled in all types of fabrics. A 100% solution consists of 20% resin and 80% water. Various auxiliaries are used for better penetration of the solution. This solution is used because it prevents the transition to a normal position and it causes wrinkles or creases.