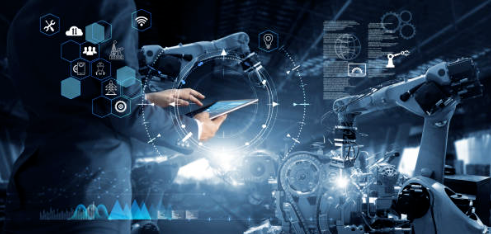
Industrial Engineering
Industrial engineering is engineering to increase productivity and quality. Here I have written about Industrial Engineering (IE) in Apparel Industry, Job Opportunities, Job Description and Basic IE Jobs in Apparel Industry.
Industrial Engineering in Apparel Industry
Garment factories are facing global competition to improve cost savings, productivity and quality. Industrial engineering deals with these issues to reach the highest level of productivity with minimum waste. So there is a great opportunity for an industrial engineer to contribute to the apparel manufacturing sector by implementing all the engineering tools for the growth of this industry.
IE team working on cutting, sewing and finishing to reduce manpower and wap, setting line layout (operation breakdown) work efficiency, productivity, demand forecasting, developing a new design, developing layout, working with different quality tools, bend products and Seasoning Development, Efficiency, Wage and Earnings Accounting, CNC Machine Operation, Scheduling, Capacity Analysis, Line Balancing, Kaizen, Kanban, Production Planning, Calculating NPT, Removing Obstacles, etc. They analyze CM, SMV, costs, expenses, profit-loss. Good IE teams make a good efficient factory. They follow daily production targets and take responsibility for production, working on the sewing line if there are any bottlenecks. Generally, textile engineers, IPE engineers, and other academic background work in the garment IE department, career growth here is very fast. After merchandising, all textile graduates go for IE jobs in garment factories. Starting a career in the IE department is not very easy, there is also a challenge and pressure to meet the production targets of the prescribed sewing line. After reaching a point, your work will give you the comfort of sitting at your desk to pursue work. This is the era of the 4th industrial revolution where people move in innovative ways to increase productivity. Importance of industrial engineering in garment industry
When garment manufacturers faced the threat of global competition, other manufacturers produced low-cost products; The garment industry began to employ industrial engineering to produce more products at lower costs. Industrial engineering works to produce maximum output with limited minimum resources and every step taken to calculate that adds value to the product.
IE Jobs in Garment Industry:
Career start in IE department as IE Officer, growing faster than any other department in garment manufacturing industry. There is a lot of work in the IE section. In recent times the garment industry has been hiring a lot of staff for engineering development at their facilities. Job titles are IE Officer, Executive, Senior Executive, Assistant Manager, Manager, Head of IE, AGM/DGM/GM
Basic knowledge of IE jobs in garments
Basic knowledge is on industrial engineering such as efficiency, production, productivity, overall efficiency, quality efficiency. Key KPIs such as Man to Machine Ratio, Cut to Ship Ratio, Order to Ship Ratio, On-Time Delivery Percentage, Average Style Change Time, Production Quality, NPT, NPT Major Areas. Skill matrix, what are the operator grading criteria. Knowledge of thread consumption, elastic, lace consumption. Identify obstacles and eliminate obstacles. Knowledge of sewing. Preparation of Operation Bulletin. Working under pressure and adapting to every situation. Dress up well and finally be smart. English knowledge is very important as there are lots of foreigners working in this sector. Mathematical knowledge like CM, CPM, EPM, efficiency, rating. Knowledge of lean, 6S, kaizen, kanban, 6M,7M,8M.etc. As an IE we have many responsibilities. Must have knowledge of IE like manpower optimization, line capacity and production study, layout setting, process analysis and process improvement efforts, bottlenecks and line balancing and target setting, elastic usage, piping and many more.
Job Responsibilities of IE Officers/Executives/Managers in Garment Industry
1. Ensure operation bulletin (OB) and re-engineer or balance bulletin for better productivity in sewing and finishing.
2. To measure accurate factory efficiency, line performance, change efficiency, capacity study, time and speed study, machine breakdown etc.
3. Carry out pre-order costs and post-order costs (artwork and samples) in coordination with merchandising team.
4. Set base targets based on basic, semi-critical and critical operations and ensure implementation of line and special incentive policies.
5. Set up SOPs, process flow charts and process re-engineering to improve various processes.
6. Conduct competency assessments of new operators, ensure floor discipline, identify training needs and manage their work standards and career development.
7. Best Use of Man, Machine and Method (3M).
8. Liaising with the product development team to make the product feasible for production while meeting customer needs.
9. Analyze productivity and improve systems by implementing kaizen and innovation in processes.
10. Prepare monthly manpower projections, requirements and turnover
11. Ensure cost reduction by reducing all forms of wastage.
12. Ensure safety, quality and compliance activities in the workplace.
13. Monitoring production schedule.
14. Study and implementation of time study, method study, etc
15. Strategic Project Planning.
16. Analyzing DFMEA and Process FMEA.
17. Monitoring worker ergonomics design for better posture
18. SMV (Standard Minutes Value), calculating efficiency and setting a target based on efficiency and SMV.
19. Implementation of Six Sigma using DMAIC methodology.
20. Adopt industrial engineering practices in every possible area for maximum productivity and ensure optimal utilization of resources and implementation of QCO.
21. Calculation of SAM by both rating method and GSD (TMIS) method
22. Must have clear knowledge of TMIS, TMIS coding system
23. Should have good knowledge of motion analysis by showing videos with TMIS software
24. Clear knowledge of Lean Tools: Kanban, Kaizen, TPM, 5S, Yamazumi Chart.
25. It is better to design production equipment/equipment considering ergonomics
26. Establish lean manufacturing culture to reduce non-value added processes.
27. Invent, update and implement methods for IE
28. Making machine layout with manpower distribution maintaining proper sequence of sewing operations to ensure optimum workflow.
29. Set up and manage training center for trainee operators, collaborate with HR for skill testing in recruitment, conduct skill assessment scheme for all production operators.
30. Good team player and high adaptability to any situation
31. Applying IE Tools and Techniques in Factory.
32. Study and record the time, pace, method and speed involved in the performance of production and other personnel activities using GSD equipment and techniques.
33. Provide costing SMV information to merchandising team for costing purposes.
34. Thread consumption
35. Set goals and draft and design layout of machines, materials, prepare layout for floor for effective utilization of men, machines and materials.
36. Resolving obstacles
37. Line Balancing
38. Follow individual orders.
39. Preparation of WPR report.
40. Capacity booking and open capacity plan as per factory business plan.
41. Check cutting production; sewing production; production completion; absence; Balance cut, loss time monitoring report; Compile reports on efficiency and work progress and production issues.
42. Cut Panel Rejection Analysis Report.
43. GSM high low observation report in cutting section.
44. Shade checking report in cutting section.
45. Transfer excess fabric saved from cutting report.
46. Prepare skill inventory for operator.
47. Arrange technical and pre-production meetings with production, quality, merchandising and PD teams before putting new styles/inputs on line.
48. Line loading plan
49. Maintaining master file from cutting to packing of all production data.
50. KPI report, follow up and annual presentation
51. Monitoring KPIs against targets.
52. Applying Lean tools (5S, Kaizen, Kanban) in various workplaces. (Administrative Office Area, QC Room, Yarn Shop, Cutting)
53. Implementation of various production and quality SOPs on the production floor (cutting, sewing and finishing).
54. Follow-up finishing WIP (from input to packing).
55. Maintenance of Left Over Status Report. Updated with ERP (ALGO ERP, LOGIC ERP).
56. Salaries of operators are made on the basis of making daily production report as per production.
57. Preparation of cutting report as per PO based on which cutting team ensures cutting.
58. Generating daily sewing WIP report as per file, PO, style and color based on which production team executes sewing.
59. Generating daily finishing WIP report by color based on which finishing team performs finishing.
60. Generating daily running order status by file, PO, and style & color to understand order status.
61. Preparation of WIP reduction report on which WIP and production progress will be known.
62. Generating washing report based on which items are being sent for washing.
63. Preparation of packing report on any CT-PAT carrying out their packing activities.
64. Creation of shipment updates to improve proper tracking of shipments.
65. Follow and strictly follow each style to generate critical shipment especially for critical shipment.
66. Reconciliation after delivery of each invoice for illustration of each invoice as per file, PO, style and color.
67. To ensure strict following of cut plan for timely cutting of cloth, by preparing cut plan follow-up report. Create and evaluate cut to ship ratio reports
68. Collecting data of all sewing lines of all units, preparing consolidated reports and variance reports and mailing to top management.
69. To identify the causes of variance between build up and actual production and resolve the issues with proper collaboration with HOO, DGM-GM and concerned persons.